In today's rapidly evolving technological landscape, the concept of "desifake" has emerged as a critical topic in modern industries. Desifake, which refers to the rise of digital fabrication techniques, is revolutionizing how products are conceptualized, designed, and manufactured. This phenomenon is reshaping traditional manufacturing processes, offering unprecedented opportunities for innovation and efficiency.
From additive manufacturing to advanced software-driven tools, digital fabrication is transforming industries across the board. The integration of these technologies is not only enhancing productivity but also enabling businesses to create complex designs that were once considered impossible.
As we delve deeper into this topic, you'll discover the significance of understanding desifake, its applications, and its impact on modern industries. By the end of this article, you'll gain a comprehensive understanding of how digital fabrication is driving the future of manufacturing.
Read also:March Madness Today Your Ultimate Guide To The Hottest Tournament Action
Before we proceed, here's a quick overview of the content we will cover:
Table of Contents
- What is Desifake?
- History of Digital Fabrication
- Key Technologies in Digital Fabrication
- Applications in Modern Industries
- Advantages of Desifake
- Challenges and Limitations
- Future Trends in Digital Fabrication
- Case Studies: Success Stories in Desifake
- Ethical Considerations in Digital Fabrication
- Conclusion and Call to Action
What is Desifake?
Desifake refers to the convergence of design and fabrication in the digital realm, enabling the creation of complex products through advanced technologies. This concept encompasses various techniques, including 3D printing, CNC machining, and laser cutting, among others.
The rise of desifake has been fueled by advancements in software and hardware, making it possible to produce high-quality goods with minimal waste. This approach is particularly valuable in industries such as aerospace, automotive, and healthcare, where precision and customization are essential.
In essence, desifake represents a paradigm shift in manufacturing, moving away from traditional methods and embracing digital solutions that enhance efficiency and innovation.
History of Digital Fabrication
Origins of Digital Fabrication
The origins of digital fabrication can be traced back to the mid-20th century when early computer-aided design (CAD) systems were developed. These systems laid the foundation for the integration of technology into manufacturing processes.
Over the decades, advancements in computing power and software capabilities have propelled digital fabrication to new heights. The introduction of 3D printing in the 1980s marked a significant milestone, opening up possibilities for rapid prototyping and production.
Read also:Watch March Madness
Modern Developments
Today, digital fabrication technologies are more accessible than ever, with affordable desktop 3D printers and user-friendly software available to both professionals and hobbyists. This democratization of technology has spurred innovation across various sectors.
According to a report by Grand View Research, the global digital fabrication market is expected to grow at a CAGR of 14.3% from 2022 to 2030, driven by increasing demand for customized products and sustainable manufacturing practices.
Key Technologies in Digital Fabrication
3D Printing
3D printing, also known as additive manufacturing, is one of the most prominent technologies in digital fabrication. It involves creating three-dimensional objects by layering materials based on digital models.
- Wide range of materials, including plastics, metals, and ceramics.
- Ability to produce complex geometries with high precision.
- Cost-effective for small-scale production and prototyping.
CNC Machining
Computer Numerical Control (CNC) machining is another critical technology in digital fabrication. It uses pre-programmed software to control machine tools, enabling precise cutting and shaping of materials.
- High accuracy and repeatability in production.
- Suitable for a variety of materials, including metals and composites.
- Capable of producing large-scale components.
Applications in Modern Industries
Aerospace Industry
The aerospace industry has embraced digital fabrication to produce lightweight and durable components. For example, companies like Boeing and Airbus use 3D printing to manufacture parts for aircraft, reducing weight and improving fuel efficiency.
Healthcare Sector
In the healthcare sector, digital fabrication is revolutionizing the production of medical devices and prosthetics. Customized implants and prosthetic limbs can now be created using 3D printing, offering better fit and functionality for patients.
Automotive Manufacturing
The automotive industry leverages digital fabrication for rapid prototyping and production of complex components. This technology allows manufacturers to test and refine designs more efficiently, reducing time-to-market for new vehicles.
Advantages of Desifake
Increased Efficiency
One of the primary advantages of desifake is the significant improvement in manufacturing efficiency. By automating processes and minimizing waste, businesses can achieve higher productivity at a lower cost.
Enhanced Customization
Desifake enables greater customization, allowing manufacturers to produce unique products tailored to individual customer needs. This capability is particularly valuable in industries such as fashion and healthcare.
Sustainability
Digital fabrication promotes sustainable manufacturing practices by reducing material waste and energy consumption. This aligns with global efforts to combat climate change and promote environmental responsibility.
Challenges and Limitations
High Initial Costs
While the long-term benefits of desifake are undeniable, the initial investment required for implementing digital fabrication technologies can be substantial. This may pose a barrier for small and medium-sized enterprises (SMEs).
Material Limitations
Although the range of materials compatible with digital fabrication is expanding, certain materials remain challenging to work with using current technologies. This limitation can restrict the scope of applications in some industries.
Skill Gap
The adoption of digital fabrication requires specialized skills and expertise, which may not be readily available in the workforce. Addressing this skill gap through training and education is crucial for the widespread adoption of these technologies.
Future Trends in Digital Fabrication
AI Integration
The integration of artificial intelligence (AI) in digital fabrication is expected to enhance automation and decision-making processes. AI-driven systems can optimize production workflows, predict maintenance needs, and improve overall efficiency.
4D Printing
4D printing, an emerging technology that builds on 3D printing, involves creating objects that can change shape or function over time. This innovation holds promise for applications in smart materials and adaptive structures.
Sustainable Materials
As environmental concerns grow, the development of sustainable materials for digital fabrication is becoming a priority. Researchers are exploring biodegradable and recyclable options to reduce the ecological footprint of manufacturing processes.
Case Studies: Success Stories in Desifake
Case Study 1: GE Additive
General Electric (GE) has successfully implemented additive manufacturing in its aviation division, producing fuel nozzles for jet engines. This initiative has resulted in a 25% reduction in weight and a 50% decrease in the number of components, improving fuel efficiency and performance.
Case Study 2: Local Motors
Local Motors, a U.S.-based automotive company, has pioneered the use of 3D printing in car manufacturing. Their flagship vehicle, the Strati, was produced using a large-scale 3D printer, showcasing the potential of digital fabrication in the automotive industry.
Ethical Considerations in Digital Fabrication
Intellectual Property
The rise of digital fabrication raises concerns about intellectual property rights. As 3D printing and other technologies make it easier to replicate designs, protecting original creations becomes increasingly challenging.
Workforce Displacement
The automation enabled by digital fabrication may lead to job displacement in certain sectors. It is essential for businesses and governments to address this issue through retraining programs and policy interventions.
Environmental Impact
While digital fabrication promotes sustainability, the production of certain materials and the energy consumption of some technologies can have adverse environmental effects. Balancing innovation with environmental responsibility is a key challenge for the industry.
Conclusion and Call to Action
Understanding desifake and the rise of digital fabrication in modern industries is crucial for businesses seeking to remain competitive in a rapidly changing world. This technology offers numerous advantages, including increased efficiency, enhanced customization, and sustainability, while also presenting challenges that need to be addressed.
We invite you to explore further resources on digital fabrication and consider how these technologies can be applied in your industry. Share your thoughts and experiences in the comments below, and don't forget to explore other articles on our website for more insights into cutting-edge technologies.
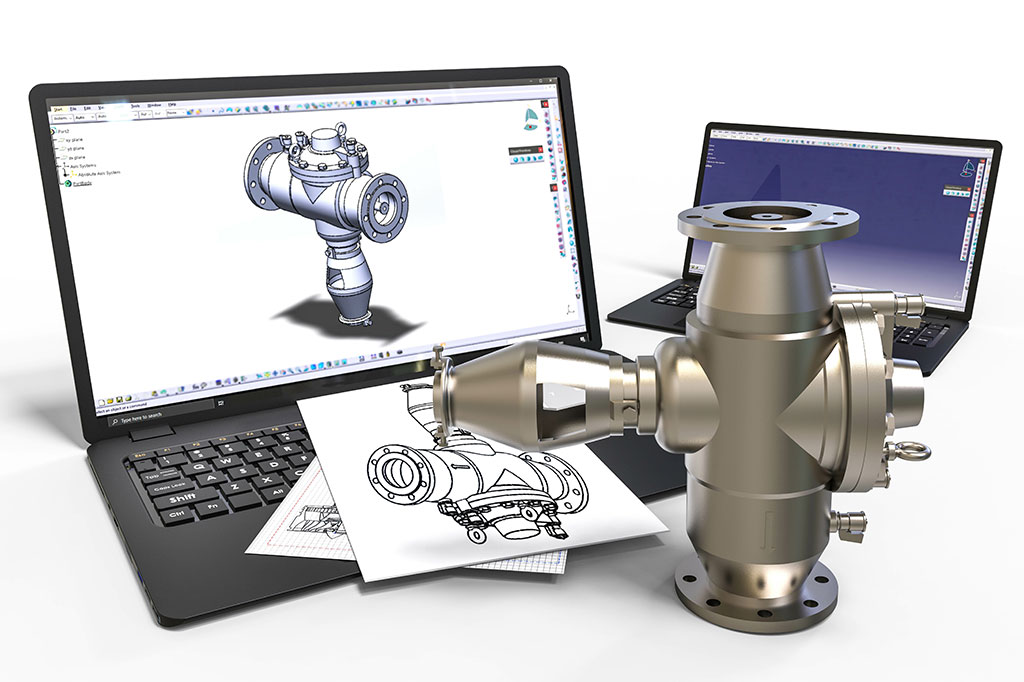
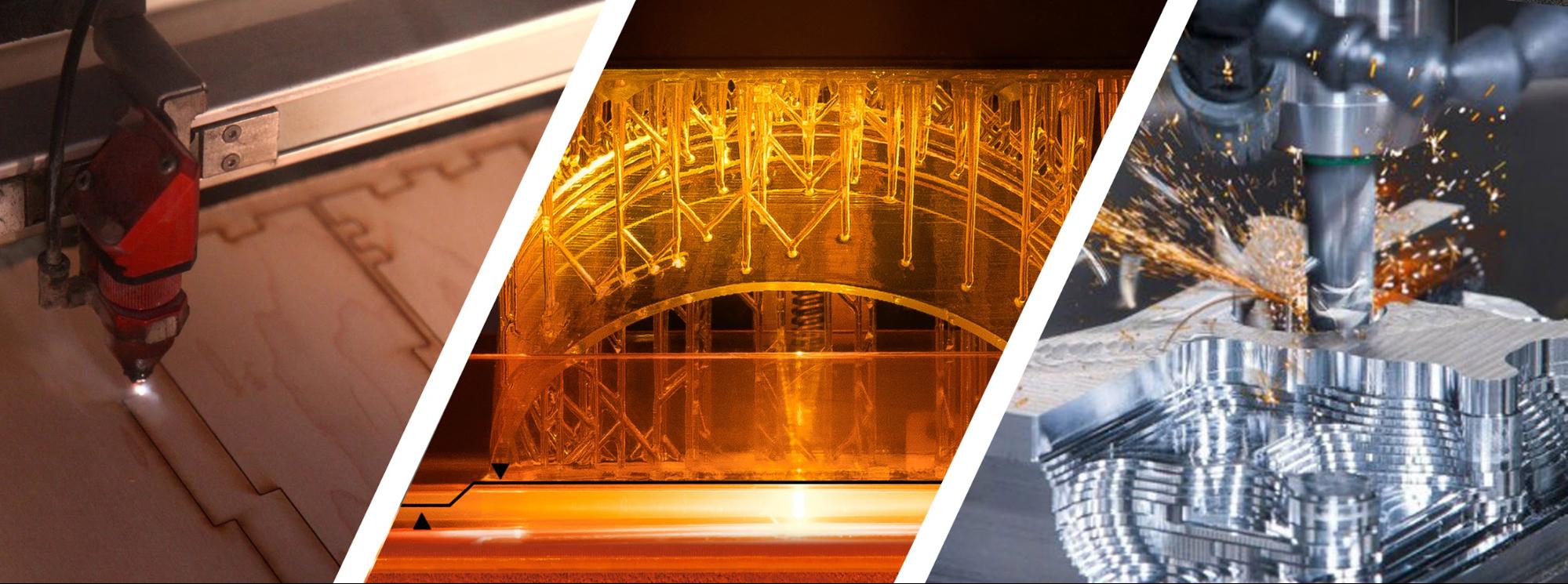
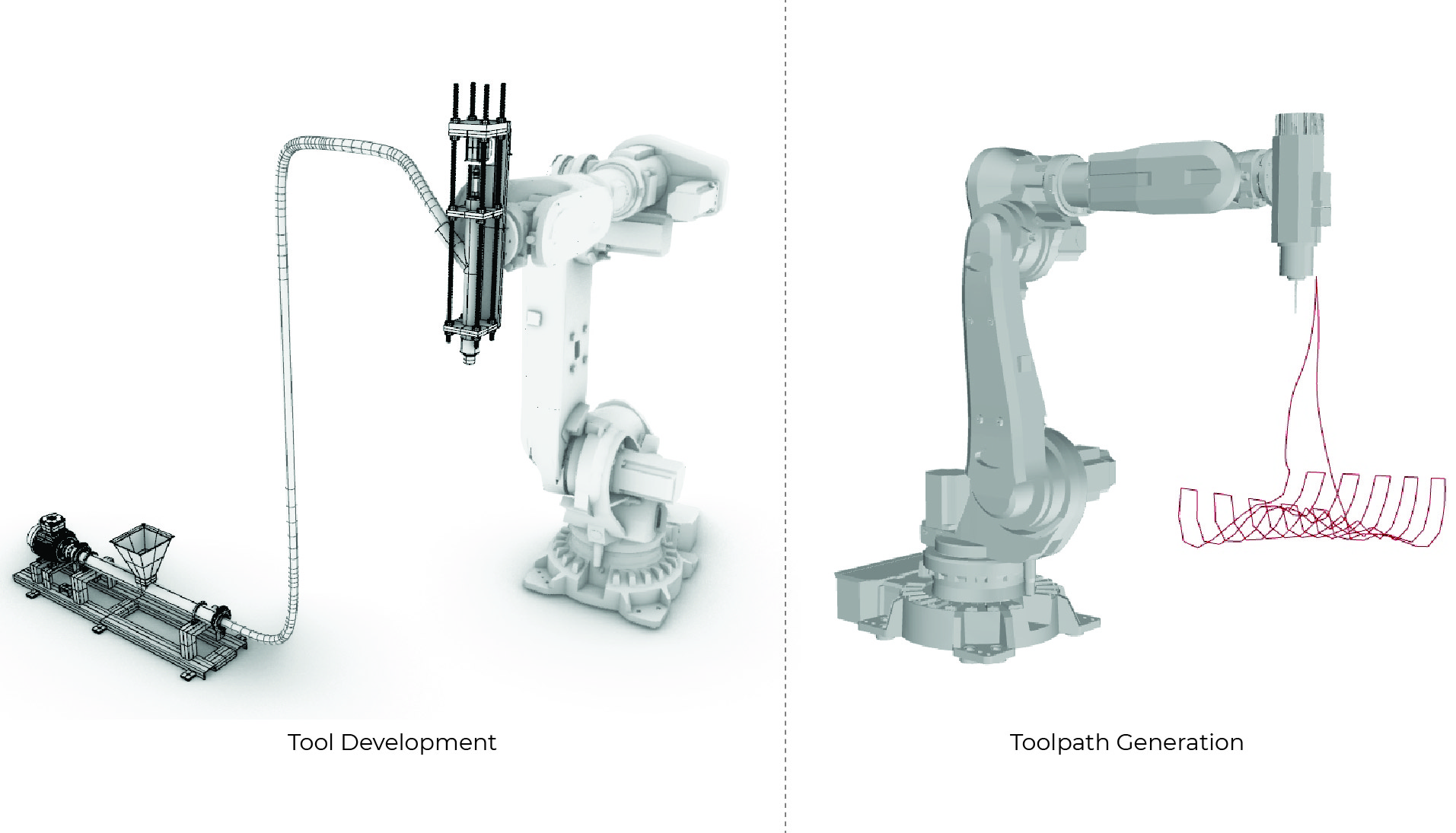